How To Build a Drone For Precision Agriculture
Introduction
Building a Low-Cost Agricultural Sprayer Drone for Precision Farming
The Agricultural Challenge
Agriculture contributes significantly to Pakistan's economy, with millions depending on farming for livelihood. While farmers in developed nations benefit from precision agriculture technologies, Pakistani farmers often lack access to these innovations due to high costs.
Pesticide application presents particular challenges:
- Manual spraying exposes farmers to harmful chemicals
- Traditional methods waste up to 50% of pesticides and water
- Tall crops and trees are difficult to spray effectively
- Conventional spraying requires extensive labor and time
- Boom sprayers can cause drift that contaminates water bodies and populated areas
Commercial agricultural drones offer solutions but at $6,000-$10,000, remain unaffordable for most local farmers.
Our Cost-Effective Solution
To bridge this technological gap, I designed and developed a low-cost octocopter drone specifically for agricultural spraying applications. The system costs approximately $3,500—less than half the price of commercial alternatives—while maintaining professional-grade performance.
Technical Specifications
The drone platform consists of:
- Frame: Octocopter configuration (eight arms) with carbon fiber construction
- Motors: Eight BLDC 6215 HD 180 KV motors for superior lift capacity
- Dimensions: 1045mm diagonal wheelbase with 386mm arm length
- Flight Controller: DJI N3 Flight Controller for stable operation
- Power: Two 6-cell 8000 mAh LiPo batteries connected in parallel
- Endurance: 10-12 minutes flight time with 8-10 minutes of active spraying
The spraying system includes:
- Tank Capacity: 5-liter fluid reservoir
- Mounting: Custom-designed 5mm acrylic mounting plate
- Pump: 12V DC self-priming pump (DP-521) with 0.65 MPa pressure
- Spray System: Multiple flat fan nozzles mounted on retractable landing gear
- Control: Arduino Nano with L298N motor driver for precise pump control
- Flow Rate: 4.0 liters per minute maximum discharge
Development Workflow
1. Virtual Simulation
Before physical implementation, I created a comprehensive simulation environment integrating:
- Robot Operating System (ROS) for data management
- Gazebo for physics-based drone simulation
- PX4 autopilot software for flight control
This virtual testing validated the design and control algorithms, ensuring the drone could handle the additional weight and dynamics of the spraying system.
2. Innovative Design Solutions
Weight management was critical for extending flight time with liquid payload. Key innovations included:
- "NO METAL" policy to minimize unnecessary weight
- Strategic positioning of components to maintain optimal center of gravity
- Nozzle placement on retractable landing gear—when the drone takes off and the landing gear retracts, nozzles automatically point downward
- Selection of flat fan nozzles for consistent 60-degree spray patterns and uniform droplet size
3. Rigorous Testing Protocol
Testing proceeded in three methodical phases:
- Basic Flight Testing: Validated drone stability and control responsiveness without spray system
- Payload Testing: Assessed flight dynamics with mounted spray system (empty tank)
- Operational Testing: Conducted spray performance evaluation with fluid in the tank at various heights
Performance Results: Twice as Fast, 83% Less Water
Mathematical analysis comparing manual spraying with drone application for one acre revealed remarkable efficiency improvements:
Parameter | Manual Spraying | Drone Spraying | Improvement |
---|---|---|---|
Time Required | 16.05 minutes | 7.49 minutes | 53% faster |
Water Used | 59.4 liters | 9.6 liters | 83% less water |
Coverage Area | 6m width per pass | 1.5m precise width | More uniform |
Health Risk | Direct exposure | Zero exposure | Significantly safer |
The drone completes the task in approximately half the time while using significantly less water—a dramatic improvement in both efficiency and sustainability.
Commercial Comparison
Model | Price (USD) | Tank Capacity | Flight Time |
---|---|---|---|
10L-608 sprayer drone | $8,500-$10,000 | 10L | 15-20 min |
TTAM6E 8L drone | $8,000-$10,000 | 8L | 10-15 min |
JT-Sprayer10 | $8,299-$9,500 | 10L | 10-15 min |
Our Model | $3,000-$3,500 | 5L | 10-15 min |
At less than half the cost of commercial alternatives, this system makes precision agriculture accessible to a much wider range of farmers.
Future Development Directions
This project establishes a foundation for accessible agricultural technology with planned enhancements:
- Increase payload capacity from 5 to 15 liters
- Extend flight endurance from 12 to 30 minutes
- Implement autonomous navigation using GPS waypoints
- Integrate multispectral cameras for NDVI analysis
- Develop variable flow rate control for precision application
Technical Insights on Spray Optimization
The system's spray effectiveness comes from careful nozzle selection and application management:
- Flat fan nozzles produce uniform droplet size at 60-degree angles
- Higher operating pressures produce smaller droplets (more drift potential)
- Larger orifices produce larger droplets (less drift)
- Optimal spray height (2m above crops) balances coverage and drift minimization
- The pump's self-priming design prevents operational failures from air binding
These technical considerations ensure maximum application efficiency while minimizing environmental impact.
Transform Your Business Today
Ready to turn challenges into competitive advantages? Let's create solutions that drive real results for your business.
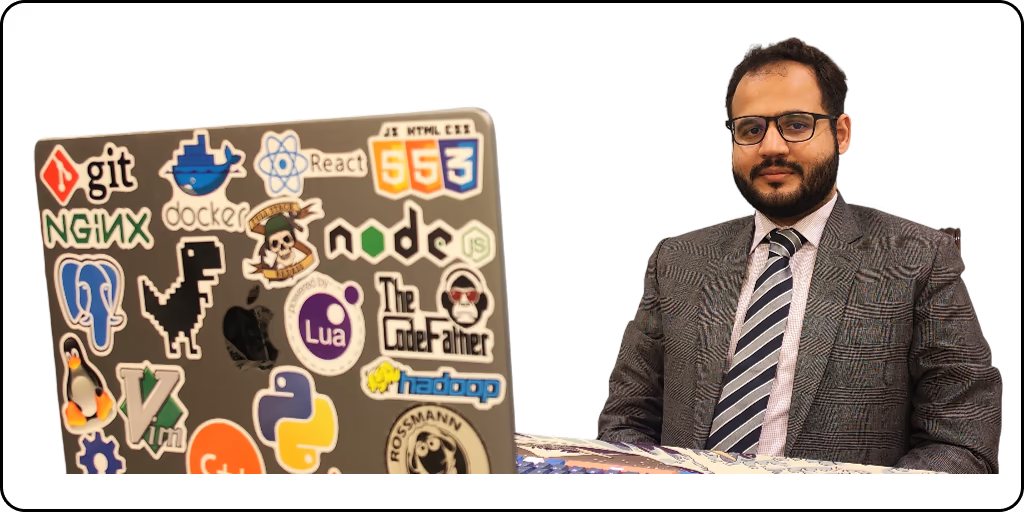
Conclusion: Democratizing Agricultural Technology
This low-cost sprayer drone demonstrates that advanced agricultural technology can be made accessible to farmers across the economic spectrum. By dramatically reducing costs while maintaining performance, we can help farmers:
- Reduce exposure to harmful chemicals
- Save substantial amounts of water and pesticides
- Increase application efficiency and crop coverage
- Apply treatments to previously inaccessible areas
Agricultural technology should serve all farmers, not just those who can afford premium solutions. This project represents a step toward democratizing precision agriculture, enabling more sustainable and profitable farming practices for all.
For technical details or to learn more about this project, you can view my complete research through my ORCID profile: 0009-0005-3034-1679.